No-Code Predictive Maintenance & Quality Control
Machine Learning for Manufacturing
Build predictive models from your manufacturing data without coding expertise. Create tools for equipment failure prediction, quality control, and production optimization using a straightforward, no-code platform.
Explore Platformuse client
Manufacturing ML Features
Platform Capabilities
Key functionalities that enable manufacturing teams to build and deploy machine learning models without specialized expertise.
Multiple
Data Types
Process time-series, categorical, and numerical data.
Various
Model Types
Classification for defect detection, regression for forecasting.
Automated
Retraining
Update models with new production data automatically.
Configurable
Alerts
Set thresholds for maintenance and quality alerts.
Production Optimization Tools
Manufacturing ML Applications
Build specific machine learning models for predictive maintenance, quality control, and production planning.
Automated Machine Learning
Upload manufacturing data and build predictive models without coding expertise.
Manufacturing Pipelines
Create reusable ML workflows that can be retrained as new production data becomes available.
Predictive Maintenance Models
Train models that predict equipment failures and maintenance needs based on sensor data.
Production Analysis Interface
Input equipment variables and receive predictions for potential failures or quality issues.
Predictive Maintenance
Machine Learning for Equipment Reliability
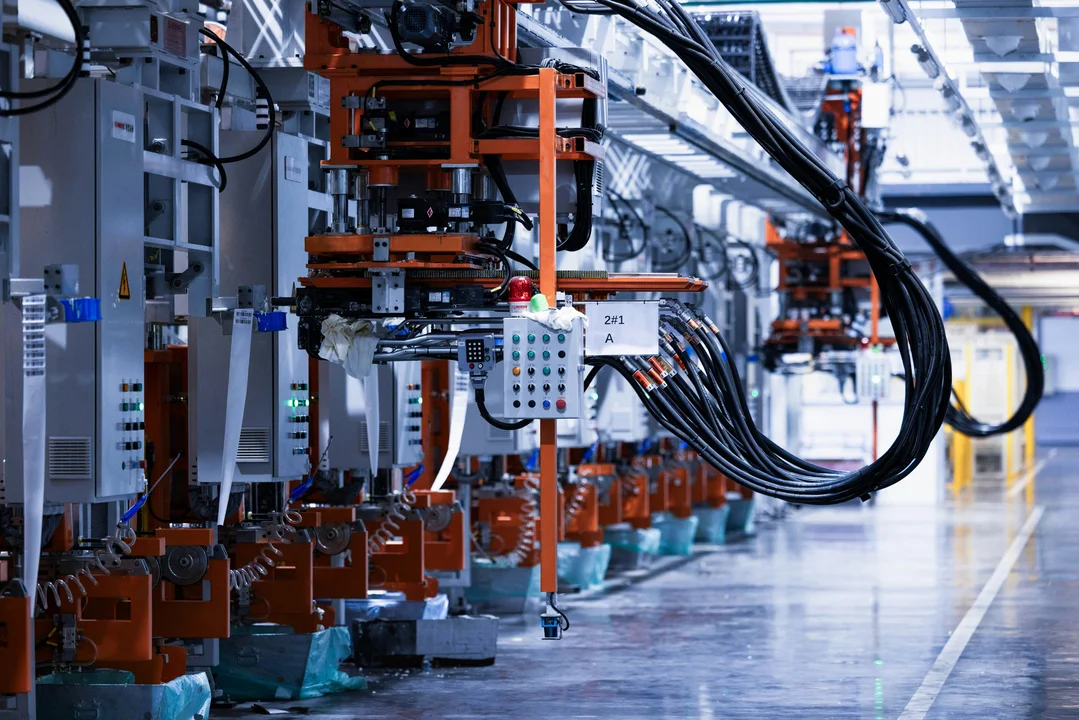
Manufacturing Use Cases
Key Applications
Specific ways manufacturing operations can use machine learning to improve efficiency and reduce costs.

Equipment Failure Prediction
Build models that analyze sensor data to predict when equipment needs maintenance before failures occur.

Quality Control Prediction
Identify factors that affect product quality and predict which production batches may have issues.

Production Output Forecasting
Forecast production capacity and resource needs based on historical patterns and current conditions.
Production Planning
Optimize Manufacturing Resources
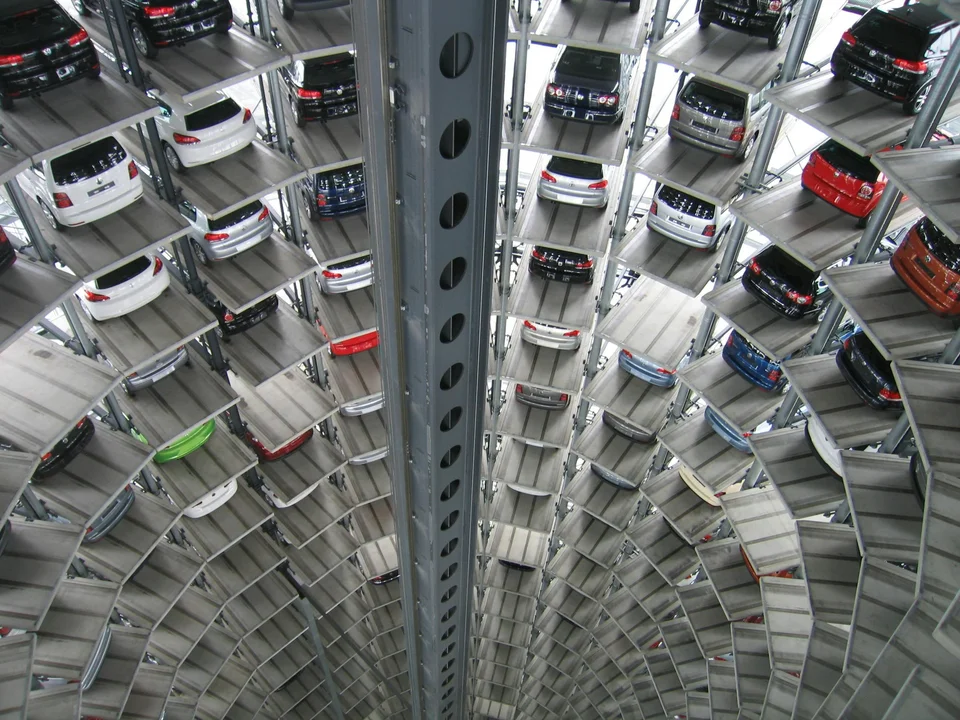
From Data to Predictions
Manufacturing ML Tools
Build, deploy, and use machine learning models specifically designed for manufacturing applications.
Predictive Maintenance Models
Train models that analyze equipment sensor data to predict failures before they happen, reducing unplanned downtime.
Make a Prediction
Prediction Result
Equipment Analysis Interface
Input current equipment parameters and receive predictions about potential failures or maintenance needs.
Production Monitoring Dashboards
Create visual displays of production metrics, equipment status, and prediction alerts for operations teams.
Automated Model Building
Upload manufacturing data and let the system build the best prediction model for your specific needs.
Quality Control
Predict Production Quality Issues
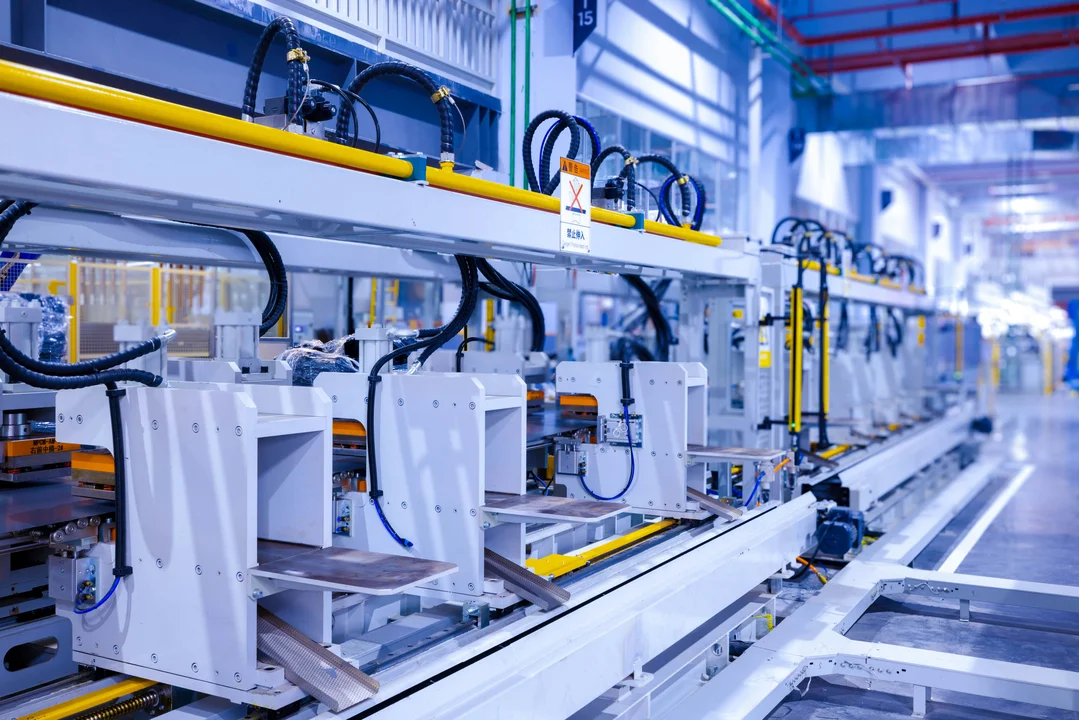
How It Works
A straightforward process for creating manufacturing prediction models without coding or data science expertise.
Data Upload
Flexible
Import CSV files with sensor and production data from your manufacturing systems.
Model Building
Automated
Select what to predict (equipment failures, quality issues) and the system handles the rest.
Deployment
Simple
Use models through the web interface or connect via API to your existing systems.
Platform Performance
Implementation Metrics
How quickly manufacturing teams can build and deploy machine learning models.
Model Building
No-Code
Create prediction models without programming.
Data Processing
Automated
Process sensor and production data automatically.
Implementation
Days
Deploy manufacturing models in days, not months.
Manufacturing Use Cases
Specific applications of machine learning in manufacturing settings using the MLClever platform.
Equipment Reliability
- Failure PredictionProactive
Identify potential equipment failures days or weeks before they occur.
- Maintenance SchedulingOptimized
Schedule maintenance when it's needed, not based on fixed intervals.
Production Efficiency
- Yield OptimizationData-Driven
Identify optimal production parameters to maximize output quality and quantity.
- Resource PlanningPredictive
Forecast material and staffing needs based on production schedules and demand.